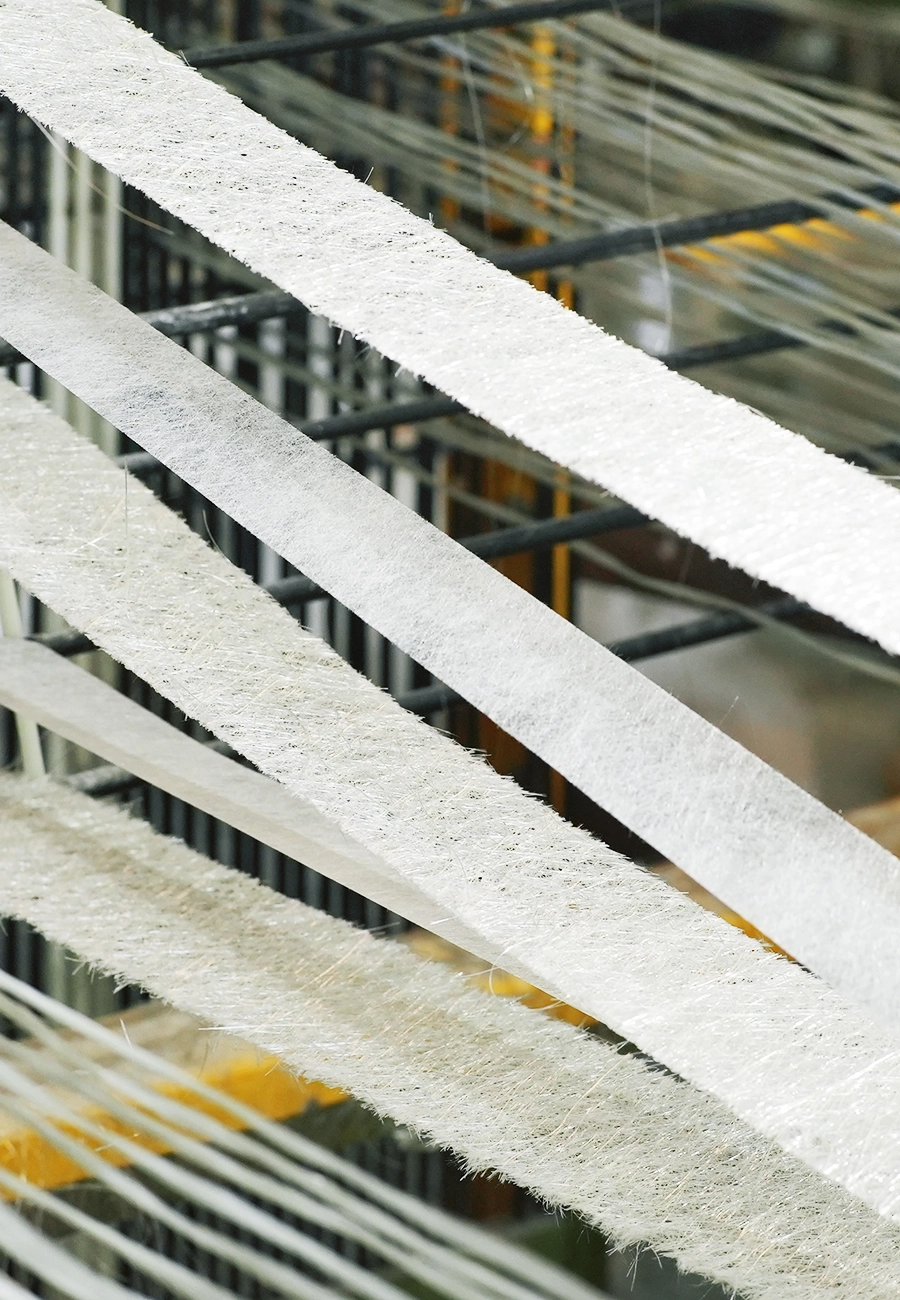
Pultrusion is one of the many composite molding methods, which produces a continuous length of material with high unidirectional strength. It is a process the continuous fiber resin enters the mold. Mainly used in the production of glass fiber, carbon fiber and other reinforced plastic products. Its advantages lie in high production efficiency, stable quality, low cost, etc., and can produce products of any length. Compared with other processes, it has the characteristics of high fiber content.
The fiber is pulled out by the creel, and other reinforcing materials can be added according to the needs to improve the transverse strength of the product.
After the resin tank is immersed in a resin and other reinforcing material, it enters the preforming unit to secure the position of the yarn bundle and drain the excess resin.
The fully impregnated fiber is heated and solidified by a traction device.
In the end the unit is cut off by the cutting machine according to the required length.
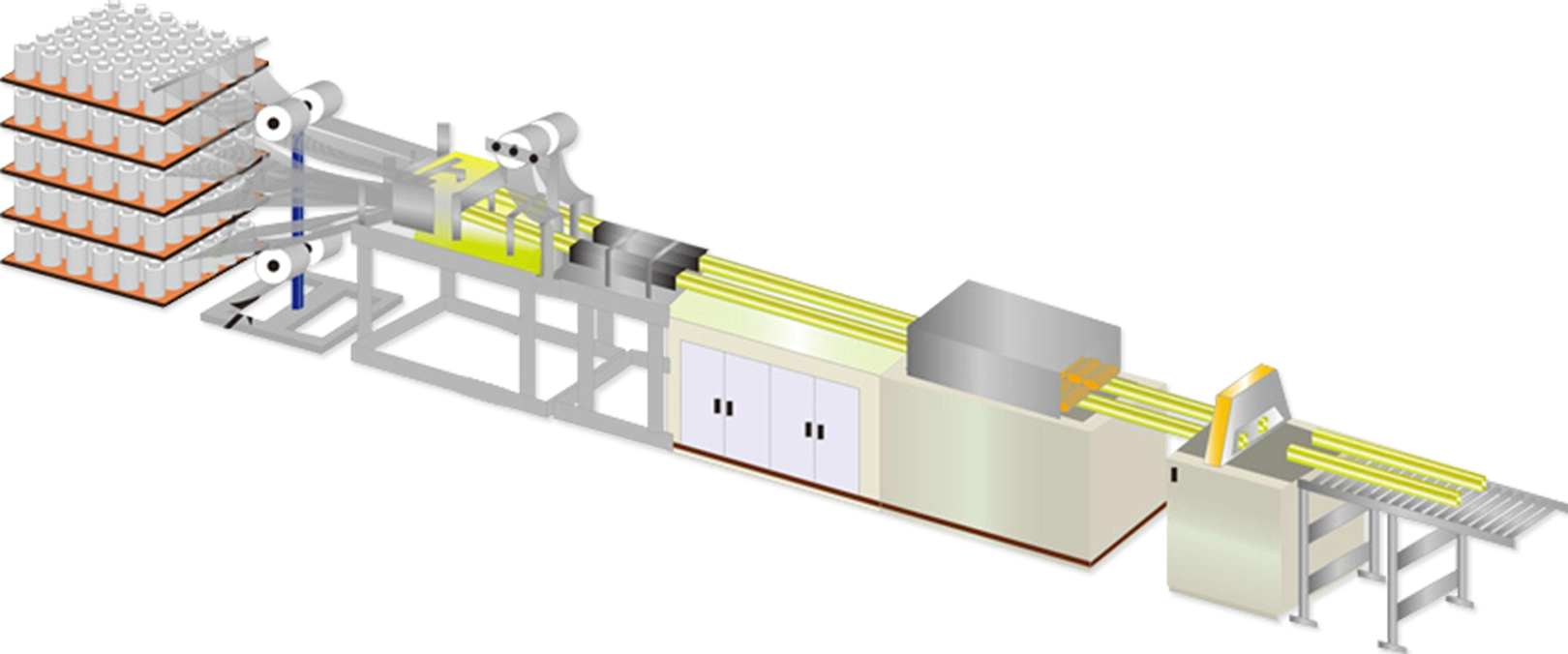
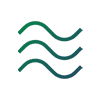
Light
Lightweight carbon fiber, glass fiber, and other composites have a specific gravity that is a quarter of steel and two-thirds that of aluminum, which can help reduce the weight of your product.
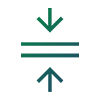
Strength
Although lighter than steel and aluminum, there is no need to sacrifice strength.
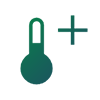
Insulation & Heat Resistance
Fiberglass is a natural insulator and has very low thermal expansion properties.
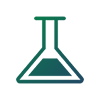
Chemical Resistance
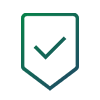
Durability
Composites have a long-life cycle and low maintenance requirements, adding value to the product.

Design Flexibility
Composite design leverages the benefits of being able to combine multiple functions into a single profile, with fiber, blanket, and resin systems to meet a wide range of challenges and requirements.